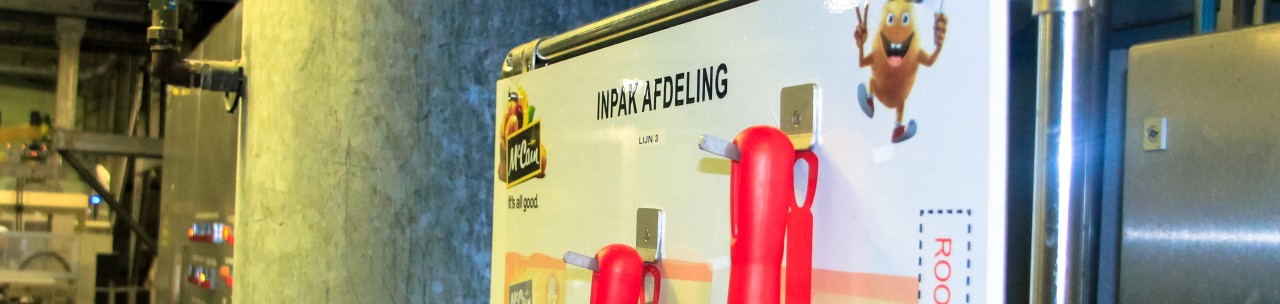
Shadow Boards help McCain Grobbendonk to keep the factory clean
McCain is a potato processing company and an international player that is represented in Europe with seven locations. In Grobbendonk, Belgium, they originally produced canned and frozen products until the production site was annexed by McCain in 1986. Since then potato specialties have been produced, from mashed potatoes to ‘kid smiles' (slices of potatoes in the form of smiley faces), from hash browns to croquettes. In short, everything except chips/French fries. The potatoes arrive fresh from the field by the truckload and leave the plant processed into frozen potato delicacies.
Preparing for lean
Marisa Geens is the McCain Competitive Edge (MCE) Manager in the McCain office in Grobbendonk. In her position she deals with the implementation of lean manufacturing in the organisation. In preparation for the steps that McCain wants to take in the future to continue to improve the production process, they are now busy laying the fundaments for this with methods such as 5S. In this context, one of the action items on her agenda is the orderly storage of cleaning materials.
Separation and storage
"We do not want the cleaning equipment in our production areas to be stored on the floor. This could cause hazardous situations because people could stumble over it, for instance", says Marisa. "Before, everything was hanging on hooks in the different production areas, but that was not sufficient because no one could see where which materials belonged. As a result, they were frequently lost or they ended up in other departments." For a food processing company such as McCain, this is taboo. “We have a department where the potatoes are supplied straight from the land. That section is partially outside, it is often sandy and muddy there. We do not want the shovels and floor squeegees of that department to end up in other departments. They could contaminate our product,” explains Marisa Geens.
Visualising creates clarity
To avoid that, the decision to use different colours had already been made earlier: black for the "dirty" sections, red for contact with the floor and blue for contact with the product itself. But the storage problem was not solved with this. Marisa took the next step according to the 5S principle and searched for shadow boards. She found them at TnP Visual Workplace. “TnP was actually the only company around that could deliver these boards tailor made and adapted to McCain’s wishes. They have helped me a lot to get everything exactly the way we wanted,” she says.
Clarity for each department
For each colour TnP Visual Workplace designed an individual board with a logo, the name of the department and an appropriate picture. The shadow boards provide a clear visual stimulus: "Each department has its own boards and the employees are responsible for it. They can now, at a glance, see what is available in their department and where the materials should be stored. Mix-ups that we want to avoid for hygienic reasons, such as a black floor squeegee on a red board, no longer occur thanks to the shadow boards. Another advantage is that it immediately stands out when the materials are not clean. That is a considerable incentive for people to keep them clean and that is the point," concludes Marisa.