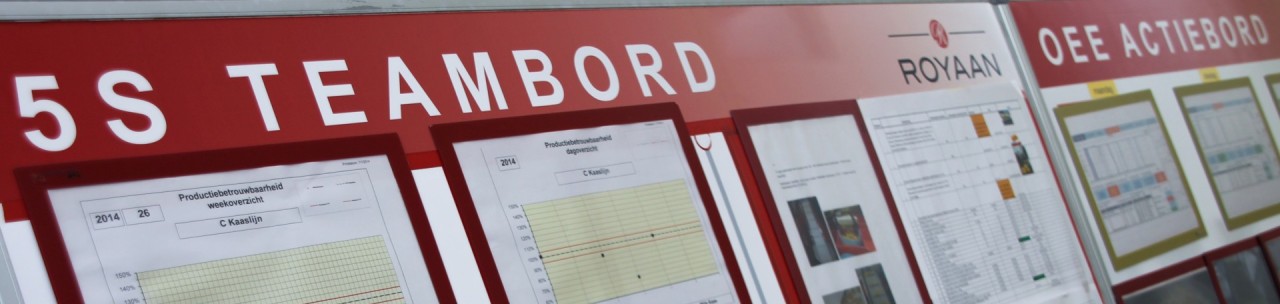
“We want our employees to feel involved”
"Your stimulator for hot snacks" is Royaan’s slogan, producer of frozen snacks for companies including McDonalds. The name will not sound familiar, but Royaan supplies for famous croquette brands in the Netherlands like Van Dobben and Kwekkeboom. The company produces at five locations in the Netherlands, including in Wijk bij Duurstede, where it is headquartered. Frans Binnenhei has been working there as manager of the production departments since 2009. For the last few years, Royaan has made good progress in implementing ‘lean’ in the different production environments.
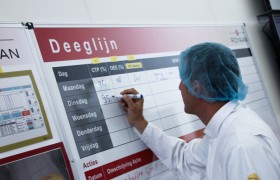
Greater sense of responsibility
“The culture within Royaan is informal and no-nonsense. We discuss what is going on directly with each other” says Binnenhei. “But what we also want is that our employees have a sense of responsibility and act in a more enterprising way on the work floor. To achieve that, we started to make clear exactly what that means; an improvement process is not only a plan that management has developed behind closed doors. It should be a daily activity for everyone in the company. Therefore, we have worked with 5S (sort, straighten, shine, standardise and sustain) as a kick-off initiative. Since then we have also increasingly developed and used lean resources, in which TnP Visual Workplace provides us with the right knowledge and products in the visual field."
Focus
In the run-up to 5S, Royaan produced an inventory of what could be improved in terms of order and cleanliness within the company. "There were dirty shoes and laundry baskets that simply overflowed with the dirty laundry, to name just one example. But also equipment whose purpose nobody knew of," recalls Frans. "We photographed everything. Those images are clear to everyone: something needs to be done. But when people are not confronted with this, you notice that the attention slackens again after the passing of time. Therefore we decided to record our progress on a big board, instead of in folders. We hung the board in the hallway, where everybody can see it, including the many temporary employees. The result is that people are keen to improve the results recorded on the board."
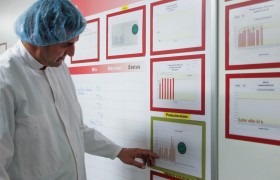
Cooperation with TnP Visual Workplace
To develop the boards, Binnenhei contacted TnP Visual Workplace. "TnP Visual Workplace helped me a great deal with the development of the boards. I was initially looking for stickers to make a board by myself but then I found TnP Visual Workplace. They could supply me with boards that were completely adapted to the needs of Royaan, with our own logo. On the internet I had seen a few examples of 5S and OEE boards, but they were all very standard. I presented my ideas to TnP Visual Workplace and on that basis they made a design. Thanks to the rapid communication back and forth, we quickly arrived at an effective board that we now use frequently."
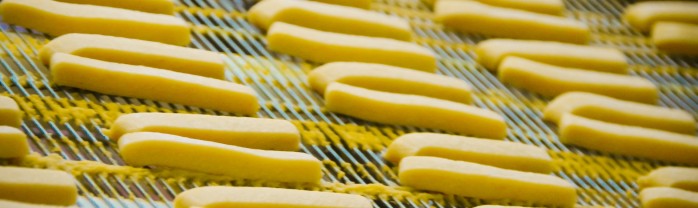
Rolling out lean
For Frans Binnenhei, lean manufacturing has become a personal passion. He was inspired by the examples from companies like Subaru that he encountered during his trips through Japan. "In a production company like this, we must constantly be improving, not only because regulations and modern production methods demand this from us, but also because we can gain benefit from it for the company," he explains. "Therefore we immediately continued with the further rollout of lean after the successful introduction of 5S. We have created working groups who have to bring in ten improvements per period.”
The success of SMED
One of those groups went to work with SMED (single minute exchange of dies), a lean-method to shorten conversion times for production. This became a huge success. Where the conversion time for the packing line was 45 minutes at first, it will now be reduced to 10 minutes or less. "Before we started this process, I made a movie of the conversion. I did this again afterwards. Those two movies speak volumes. And the good thing is that the improvements were suggested by the relevant employees themselves", says Binnenhei.
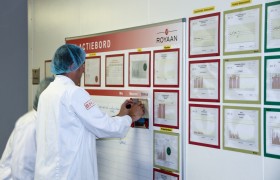
Visualising
In order to keep the process going, visualisation is necessary. "We use the boards of TnP Visual Workplace among other things during the morning meetings to review what has happened the day before, for example in terms of failures and quality. First we did this around the table, now standing in the hallway with the board. We do this deliberately so we keep the momentum going and employees who pass from the cloakrooms see that there is actually something being done about the problems they have reported. Furthermore, boards where we show what is happening in the factories are hanging in most parts of the hallways. Everyone may use these boards."
Ownership
Lean has become established within Royaan. "Many things have been achieved", says Frans Binnenhei, "but we are still not there yet. Some improvements yield time and money immediately, others are more difficult to measure. It is important that employees feel they are the owners of their own piece of the production process and take responsibility for that too".
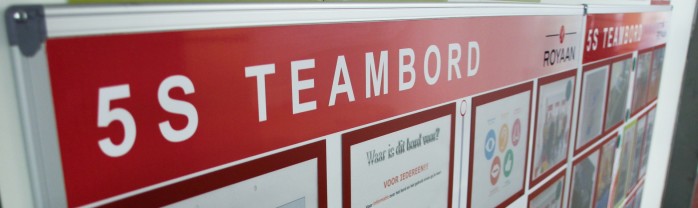